Artie Peterson resumes & CV records
Resumes
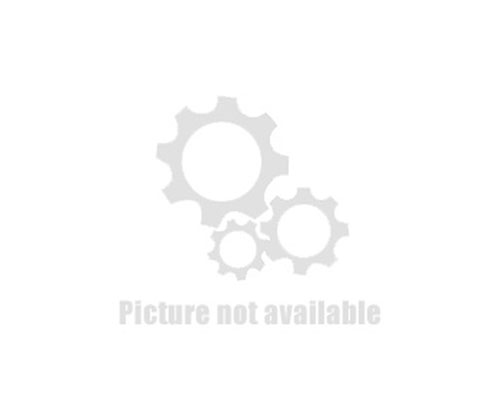
Concord, NC
Locust, NC
Harrisburg, NC
2107 Deepwood Pl NW, Concord, NC 28027 704-4600569
Mentions for Artie Gene Peterson
NOTICE: You may not use BackgroundCheck or the information it provides to make decisions about employment, credit, housing or any other purpose that would require Fair Credit Reporting Act (FCRA) compliance. BackgroundCheck is not a Consumer Reporting Agency (CRA) as defined by the FCRA and does not provide consumer reports.