Branko Lakic resumes & CV records
Resumes
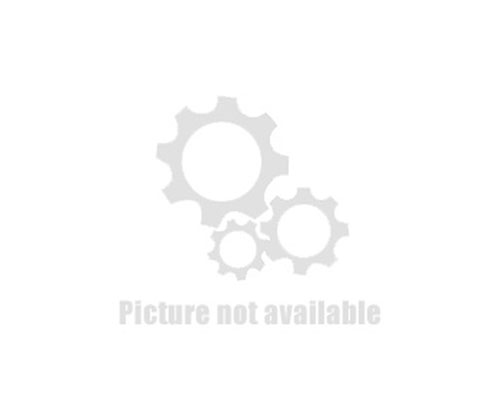
Associate Technical Fellow, Airframe Structure Design, Boeing Commercial Airplanes
Location:
Seattle, WA
Industry:
Aviation & Aerospace
Work:
Boeing
Associate Technical Fellow, Airframe Structure Design, Boeing Commercial Airplanes Palm Beach Gardens Florida 2002 - 2004
Embraer - Pbi Toronto Ontario Canada 1997 - 2000
Bombardier Aerospace
Associate Technical Fellow, Airframe Structure Design, Boeing Commercial Airplanes Palm Beach Gardens Florida 2002 - 2004
Embraer - Pbi Toronto Ontario Canada 1997 - 2000
Bombardier Aerospace
Education:
University of Belgrade
Bachelors, Bachelor of Science, Design, Aerospace Engineering
Bachelors, Bachelor of Science, Design, Aerospace Engineering
Skills:
Aerospace Engineering, Aircraft Design, Composites, Root Cause Analysis, Catia
Interests:
Tennis
Languages:
English
Serbian
Serbian
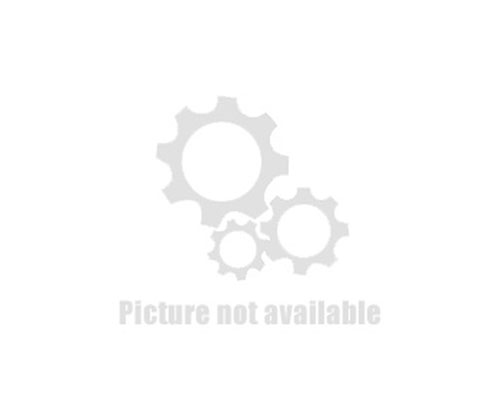
Branko Lakic
Location:
Kirkland, WA
Work:
Boeing
Senior Principal Airplane Structure Design Engineer
Senior Principal Airplane Structure Design Engineer
Skills:
Structures, Engineering, Design