Career records & work history
Lawyers & Attorneys
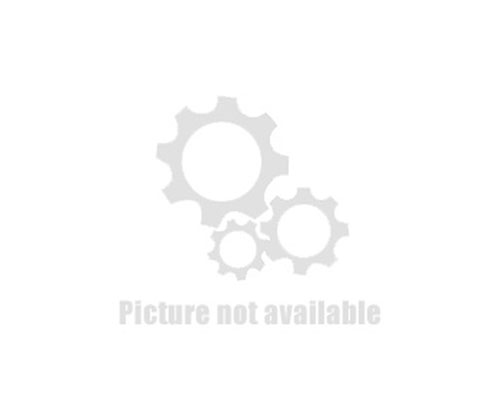
26342 Spring Creek Cir, Lake Forest, CA 92630
12425 Dido Vista Ct, Fort Worth, TX 76179 817-2368530
4217 Hahn Blvd, Haltom City, TX 76117
4305 Hahn Blvd, Haltom City, TX 76117
Argyle, TX
East Haven, CT
Plano, TX
Mentions for Frank C Romeo
NOTICE: You may not use BackgroundCheck or the information it provides to make decisions about employment, credit, housing or any other purpose that would require Fair Credit Reporting Act (FCRA) compliance. BackgroundCheck is not a Consumer Reporting Agency (CRA) as defined by the FCRA and does not provide consumer reports.