Jeffrey Maling resumes & CV records
Resumes
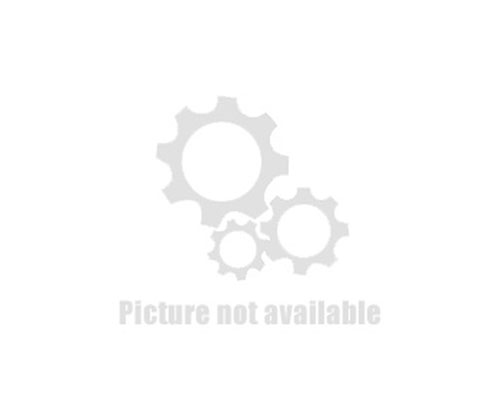
22 Moccasin Ave, Grand Isle, VT 05458 802-3725181
204 Margaret St #B, Plattsburgh, NY 12901 518-4622322 802-3725181
204 Margaret St, Plattsburgh, NY 12901
70 Broad St, Plattsburgh, NY 12901 518-4622322 802-3725181
105 Fales Ct, Troy, NY 12180 518-2701878
62 Timberline Dr, Poughkeepsie, NY 12603 845-4622322
Arlington, NY
Mentions for Jeffrey C Maling
NOTICE: You may not use BackgroundCheck or the information it provides to make decisions about employment, credit, housing or any other purpose that would require Fair Credit Reporting Act (FCRA) compliance. BackgroundCheck is not a Consumer Reporting Agency (CRA) as defined by the FCRA and does not provide consumer reports.