Career records & work history
Real Estate Brokers
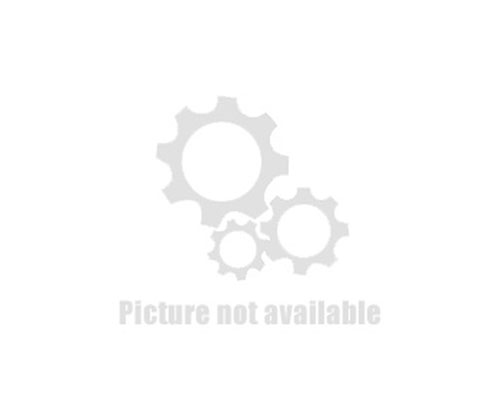
Bruiser
Specialties:
Buyer's Agent, Listing Agent
Work:
Freds Rockin Rollers
123 Happy Lane
303-2548513 (Office)
123 Happy Lane
303-2548513 (Office)
Medicine Doctors
Jen J. Lin
Specialties:
Pediatric Nephrology
Work:
Wake Forest Baptist Health Pediatric Nephrology
Medical Ctr Blvd Meads Hall, Winston Salem, NC 27157
336-7164663 (phone) 336-7134501 (fax)
Medical Ctr Blvd Meads Hall, Winston Salem, NC 27157
336-7164663 (phone) 336-7134501 (fax)
Education:
Medical School
Taipei Med Coll, Taipei, Taiwan (385 04 Prior 1/71)
Graduated: 1980
Taipei Med Coll, Taipei, Taiwan (385 04 Prior 1/71)
Graduated: 1980
Procedures:
Dialysis Procedures
Conditions:
Acute Upper Respiratory Tract Infections, Anemia, Congenital Anomalies of the Heart, Constipation, Dehydration, Hemolytic Anemia, Otitis Media, Pneumonia, Sickle-Cell Disease, Skin and Subcutaneous Infections, Urinary Incontinence, Vitamin D Deficiency
Languages:
English
Description:
Dr. Lin graduated from the Taipei Med Coll, Taipei, Taiwan (385 04 Prior 1/71) in 1980. He works in Winston-Salem, NC and specializes in Pediatric Nephrology. Dr. Lin is affiliated with Wake Forest Baptist Medical Center.