Career records & work history
Lawyers & Attorneys
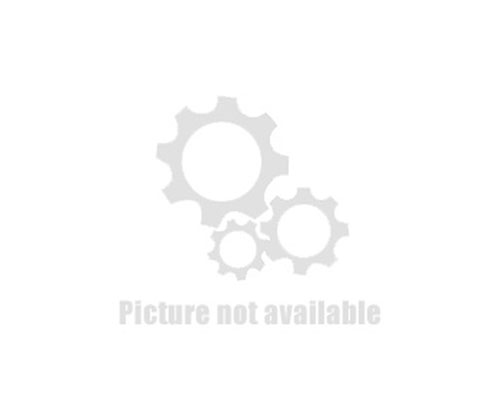
John Slagter - Lawyer
Office:
Tucker Ellis, LLP
Specialties:
Real Estate & Construction, Litigation, Oil & Gas, Business Law, Commercial Law, Education & School Law, Environmental Law, Real Property, Government Relations & Advisory, Land Use & Zoning, Commercial Law, Public and Public Finance, Banking and Commercial
ISLN:
901460873
Admitted:
1991
University:
John Carroll University, Cleveland, Ohio, B.A., 1988
Law School:
Case Western Reserve University School of Law, Cleveland, Ohio, J.D., 1991