Karen Badger resumes & CV records
Resumes
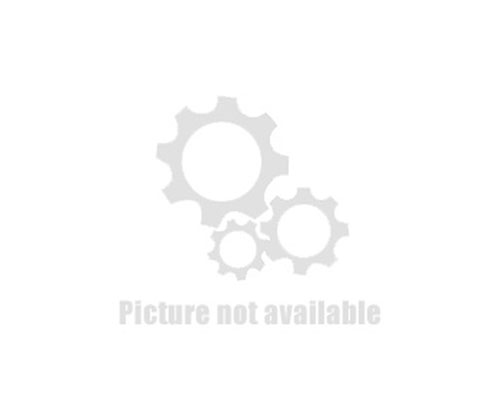
Advisory Engineer
Location:
1163 Decker Rd, Milton, VT 05468
Industry:
Semiconductors
Work:
Globalfoundries
Advisory Engineer Ibm Sep 1978 - Jun 2015
Advisory Engineer Badger Bliss Books Sep 1978 - Jun 2015
Author and Chief Executive Officer
Advisory Engineer Ibm Sep 1978 - Jun 2015
Advisory Engineer Badger Bliss Books Sep 1978 - Jun 2015
Author and Chief Executive Officer
Education:
St. Michaels's College 1984 - 1994
Bachelors, Mathematics Saint Michael's College 1974 - 1994
Bachelors, Bachelor of Science, Mathematics University of Vermont
Rice Memorial High School
Saint Michael's College
Bachelors, Bachelor of Arts, Elementary Education, Theatre
Bachelors, Mathematics Saint Michael's College 1974 - 1994
Bachelors, Bachelor of Science, Mathematics University of Vermont
Rice Memorial High School
Saint Michael's College
Bachelors, Bachelor of Arts, Elementary Education, Theatre
Skills:
Linux, Unix, Agile Methodologies, Software Development, Testing, Java, C++, C, Xml, Sql, Virtualization, Perl, Clearcase, Shell Scripting
Interests:
Camping
Motorcycling
Writing
Kayaking
Motorcycling
Writing
Kayaking
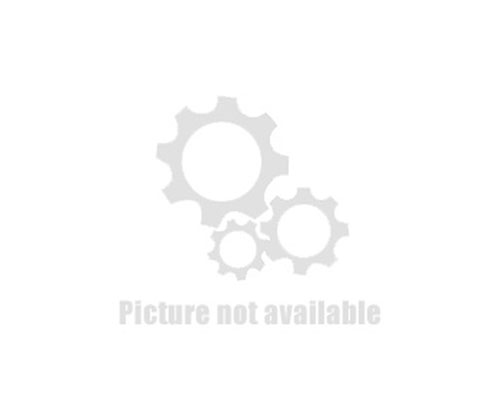
Karen Badger
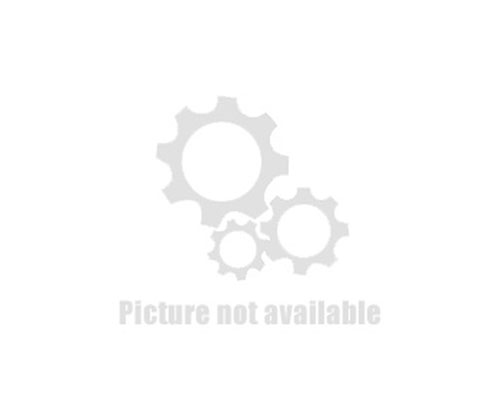
Karen Badger
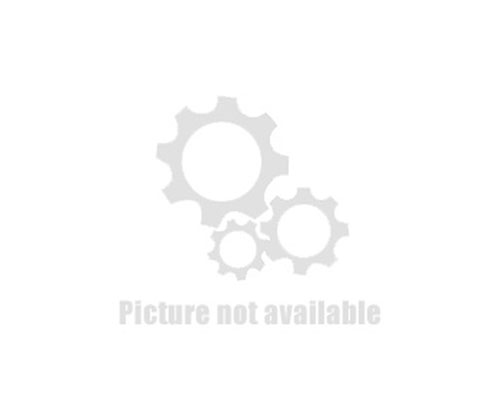
Karen Badger
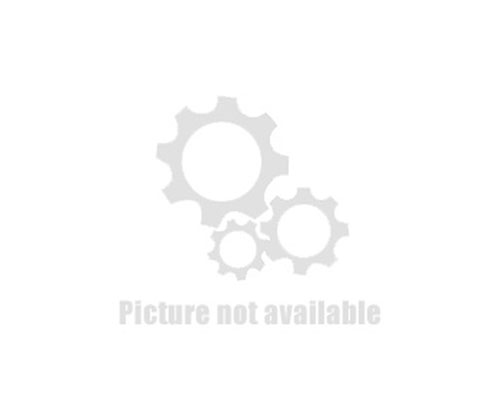
Karen Badger
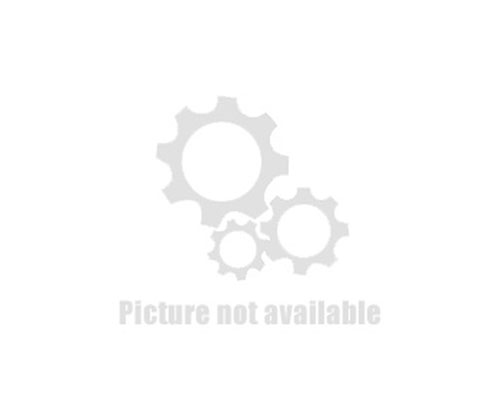
Karen Badger
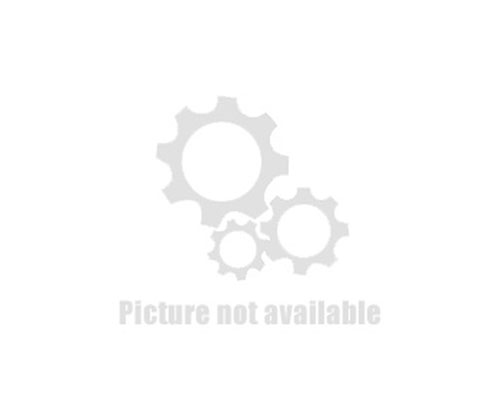
Bookkeeper At Paper Trail Bookkeeping
Location:
Burlington, Vermont Area
Industry:
Accounting
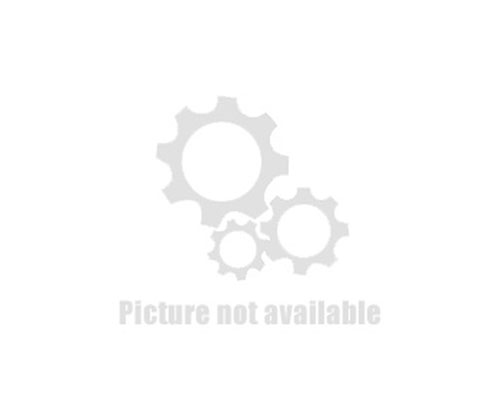
Karen Badger
Location:
United States