Resumes & CV records
Resumes
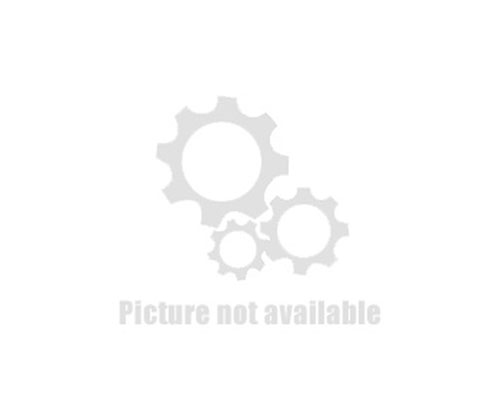
Mark Southwood
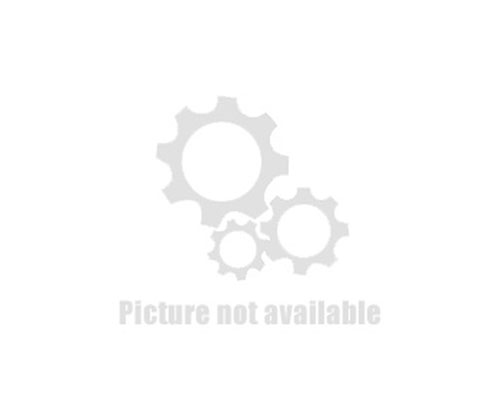
Mark Southwood
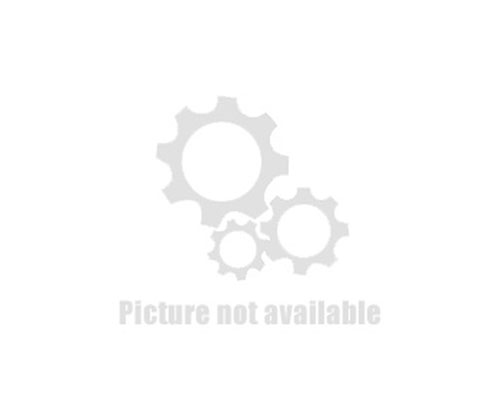
12916 39Th St, Vancouver, WA 98685 360-5734820 360-2580823
12916 39Th Ave, Vancouver, WA 98685 360-5734820 360-2580823
Bozeman, MT
Moses Lake, WA
Townsend, MT
12916 NW 39Th Ave, Vancouver, WA 98685
Mentions for Mark E Southwood
NOTICE: You may not use BackgroundCheck or the information it provides to make decisions about employment, credit, housing or any other purpose that would require Fair Credit Reporting Act (FCRA) compliance. BackgroundCheck is not a Consumer Reporting Agency (CRA) as defined by the FCRA and does not provide consumer reports.