Nicholas Giammarco resumes & CV records
Resumes
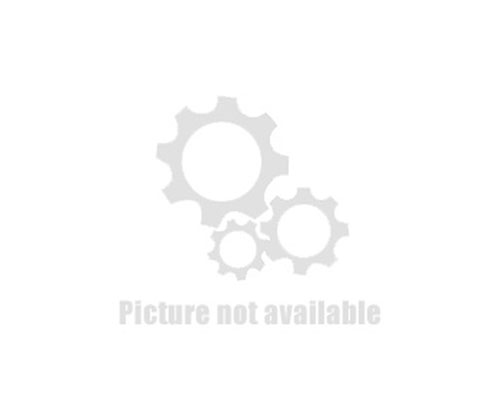
Marketing Consultant
Location:
Newburgh, NY
Industry:
Semiconductors
Work:
Lam Research
Nov 2005 - Mar 2013
General Manager Nick Giammarco Consulting Nov 2005 - Mar 2013
Marketing Consultant
General Manager Nick Giammarco Consulting Nov 2005 - Mar 2013
Marketing Consultant
Skills:
Semiconductors, Semiconductor Industry, Process Improvement, Design of Experiments, Cross Functional Team Leadership, Contract Negotiation, Spc, Thin Films, Engineering Management, Program Management, Business Process, Strategic Planning, Strategy, Metrology, Manufacturing, Electronics, Lean Manufacturing, Process Simulation, Ic, Characterization, Failure Analysis
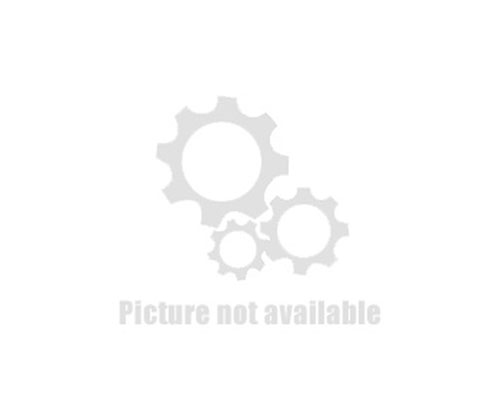
Investment Assistant
Location:
Newburgh, NY
Work:
Citizens Investment Services
Investment Assistant
Investment Assistant
Education:
Rhode Island College 2014 - 2019
Bachelors, Bachelor of Science
Bachelors, Bachelor of Science