Robert Mctigue resumes & CV records
Resumes
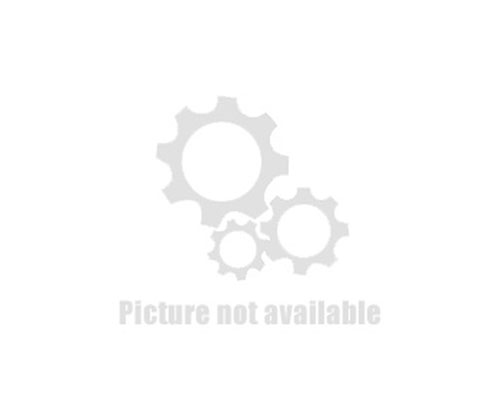
Robert Mctigue
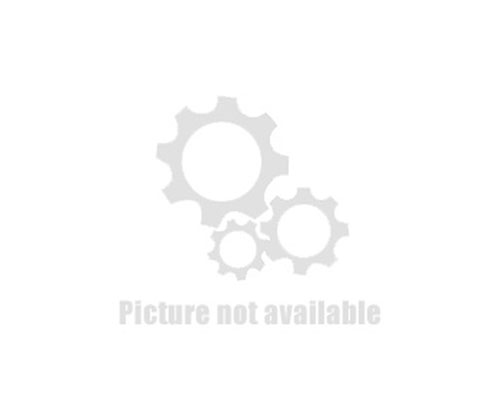
161 Beverly Rd, Chester, NY 10918 914-7416643
26 Hartford Ave, Greenwich, CT 06830 203-5320414
123 Broadway, Pleasantville, NY 10570 914-7416643
New City, NY
Albany, NY
Mentions for Robert P Mctigue
NOTICE: You may not use BackgroundCheck or the information it provides to make decisions about employment, credit, housing or any other purpose that would require Fair Credit Reporting Act (FCRA) compliance. BackgroundCheck is not a Consumer Reporting Agency (CRA) as defined by the FCRA and does not provide consumer reports.