Adam Ditzler resumes & CV records
Resumes
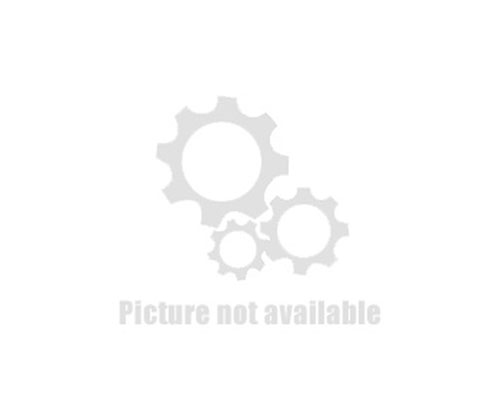
Chief Engineer, Landing Gear
Chief Engineer, Landing Gear Utc Aerospace Systems Mar 2012 - Jan 2018
Chief Design and Innovation Engineer, Landing Gear Goodrich Landing Gear Mar 2010 - Apr 2012
Principal Engineer - Design and Innovation Goodrich Landing Gear Mar 2009 - Mar 2010
Technology Project Engineer Goodrich Landing Gear May 1991 - Mar 2009
Senior Design Engineer Menasco 1991 - 1999
Senior Design Engineer, Landing Gear General Dynamics 1988 - 1991
Engineer, Landing Gear
Bachelor of Science In Mechanical Engineering, Bachelors, Mechanical Engineering