Stephen Abel resumes & CV records
Resumes
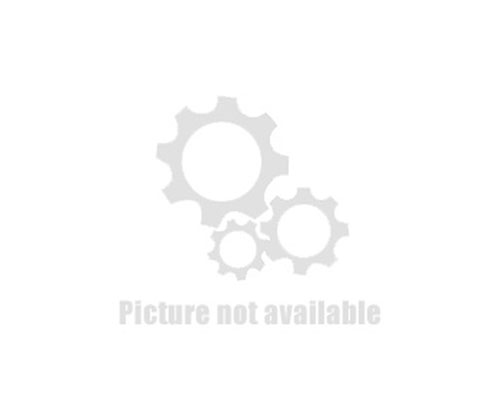
Stephen Abel
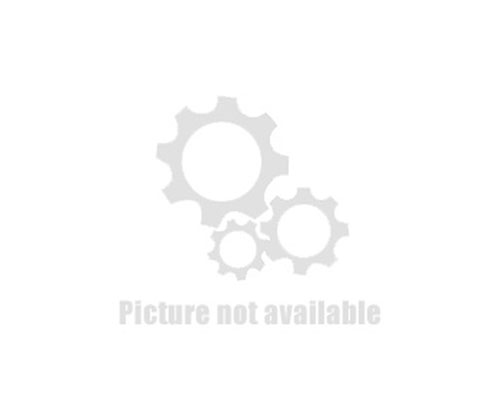
Stephen Abel
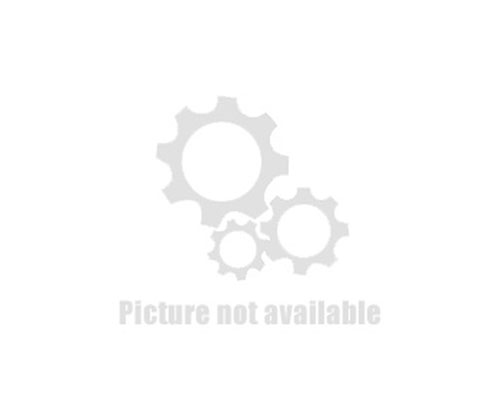
Stephen Abel
Location:
United States
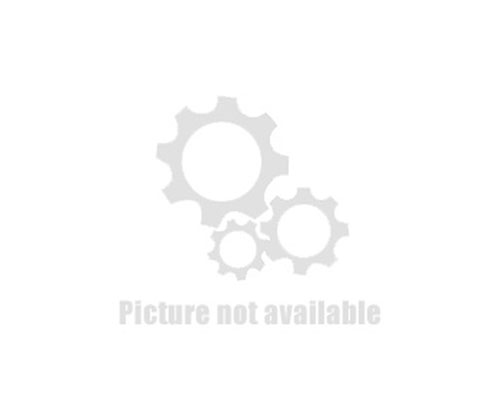
Stephen Abel
Location:
United States
Greeley, CO
Grand Junction, CO
Clifton, CO
Clarkdale, AZ
Glendale, AZ
Flagstaff, AZ
Black Canyon City, AZ
Mentions for Stephen Abel
NOTICE: You may not use BackgroundCheck or the information it provides to make decisions about employment, credit, housing or any other purpose that would require Fair Credit Reporting Act (FCRA) compliance. BackgroundCheck is not a Consumer Reporting Agency (CRA) as defined by the FCRA and does not provide consumer reports.