Career records & work history
Lawyers & Attorneys
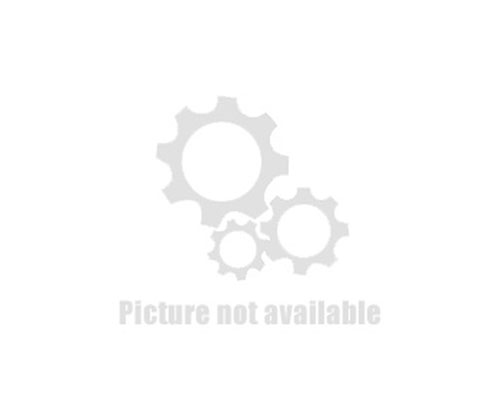
Steven Walton - Lawyer
ISLN:
924178120
Admitted:
2011
158 Shawmut Ave, Marlborough, MA 01752 508-4855965
Kent, WA
Renton, WA
Mentions for Steven R Walton
NOTICE: You may not use BackgroundCheck or the information it provides to make decisions about employment, credit, housing or any other purpose that would require Fair Credit Reporting Act (FCRA) compliance. BackgroundCheck is not a Consumer Reporting Agency (CRA) as defined by the FCRA and does not provide consumer reports.