Career records & work history
Real Estate Brokers
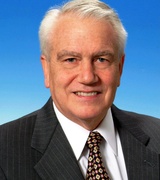
Agent
7234 Lancaster Pk
302-2393000 (Office), 302-7657783 (Cell)
Lawyers & Attorneys
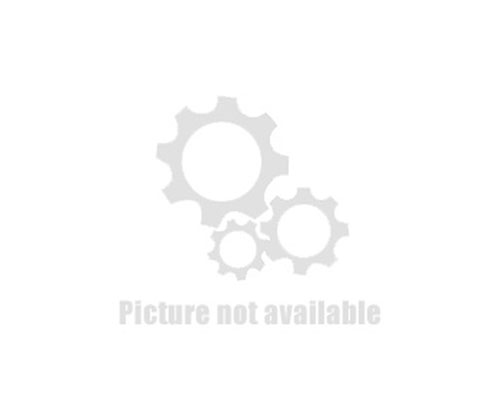
William Eakins - Lawyer
License Records
William A. Eakins
Category: Real Estate
Type: Resident Salesperson
Coventry, CT
North Adams, MA
123 Woodland Ave, Bloomfield, CT 06002 860-2430845
372 Phaeton St, Windsor, CT 06095 860-2980235
403 Broad St, Windsor, CT 06095 860-2199532 860-2988803
45 Tunxis St, Windsor, CT 06095
Signal Mountain, TN
Providence, RI
Steamboat Springs, CO
123 Woodland Ave, Bloomfield, CT 06002
Mentions for William John Eakins
NOTICE: You may not use BackgroundCheck or the information it provides to make decisions about employment, credit, housing or any other purpose that would require Fair Credit Reporting Act (FCRA) compliance. BackgroundCheck is not a Consumer Reporting Agency (CRA) as defined by the FCRA and does not provide consumer reports.