William Scheib resumes & CV records
Resumes
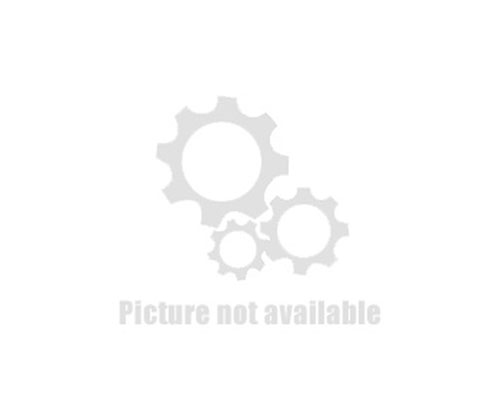
Process Engineer
Process Engineer Bombardier
Primary Systems Engineer and Gear Expert
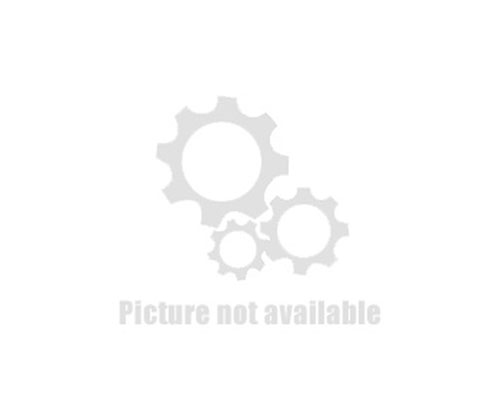
Continuous Improvement Manager At B&W Clinch River
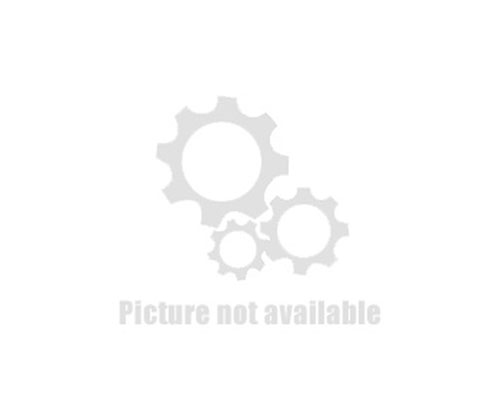
9143 Longcroft Dr, White Lake, MI 48386 248-3604375
9570 Crown Ridge Dr, White Lake, MI 48386 248-8918735
Bethel Park, PA
Pittsburgh, PA
Haines City, FL
Seven Hills, OH
Pontiac, MI
Lennon, MI
Commerce Township, MI
4121 Braidwood Dr, White Lake, MI 48383 248-8953621
Mentions for William A Scheib
NOTICE: You may not use BackgroundCheck or the information it provides to make decisions about employment, credit, housing or any other purpose that would require Fair Credit Reporting Act (FCRA) compliance. BackgroundCheck is not a Consumer Reporting Agency (CRA) as defined by the FCRA and does not provide consumer reports.